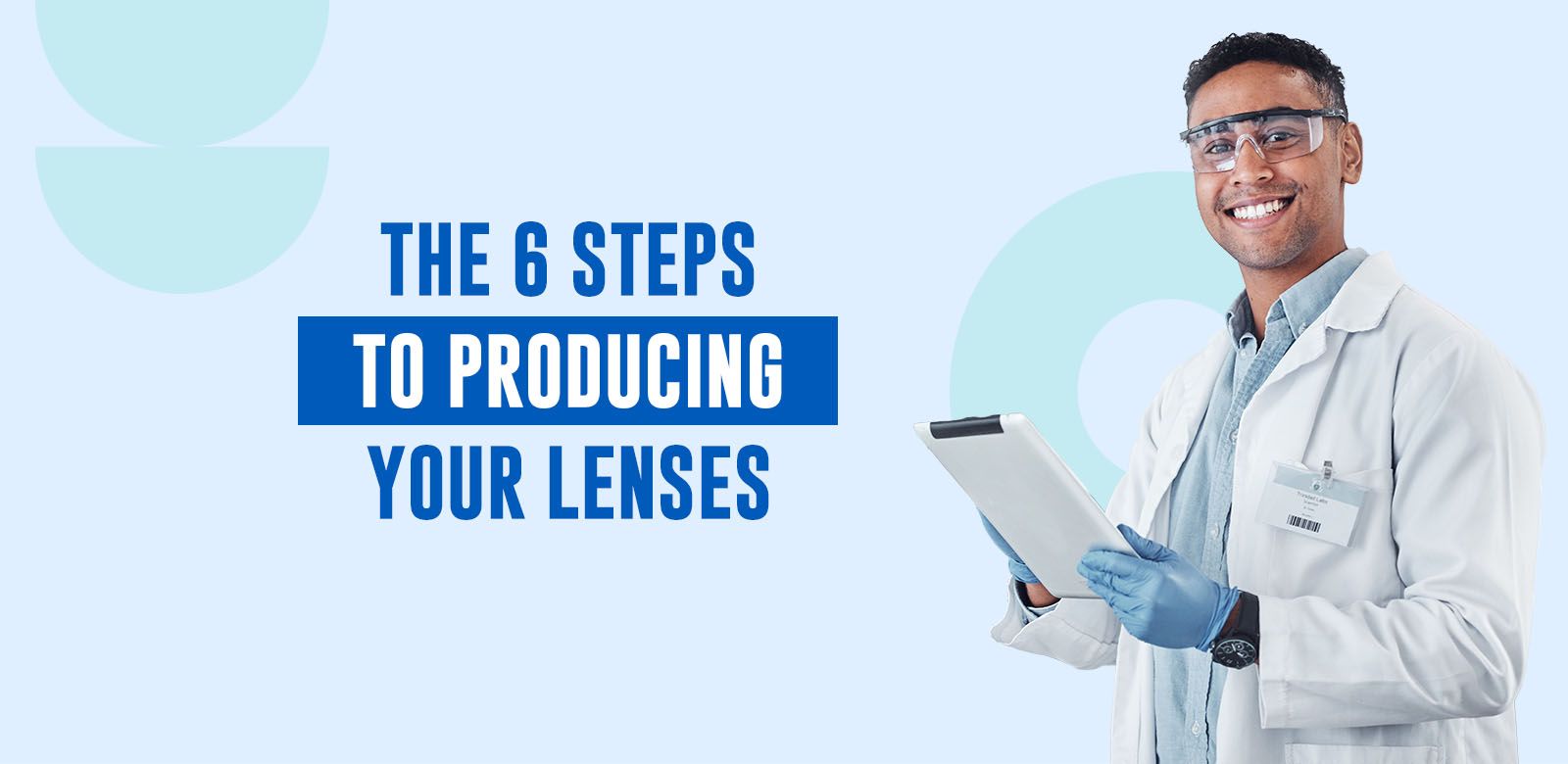
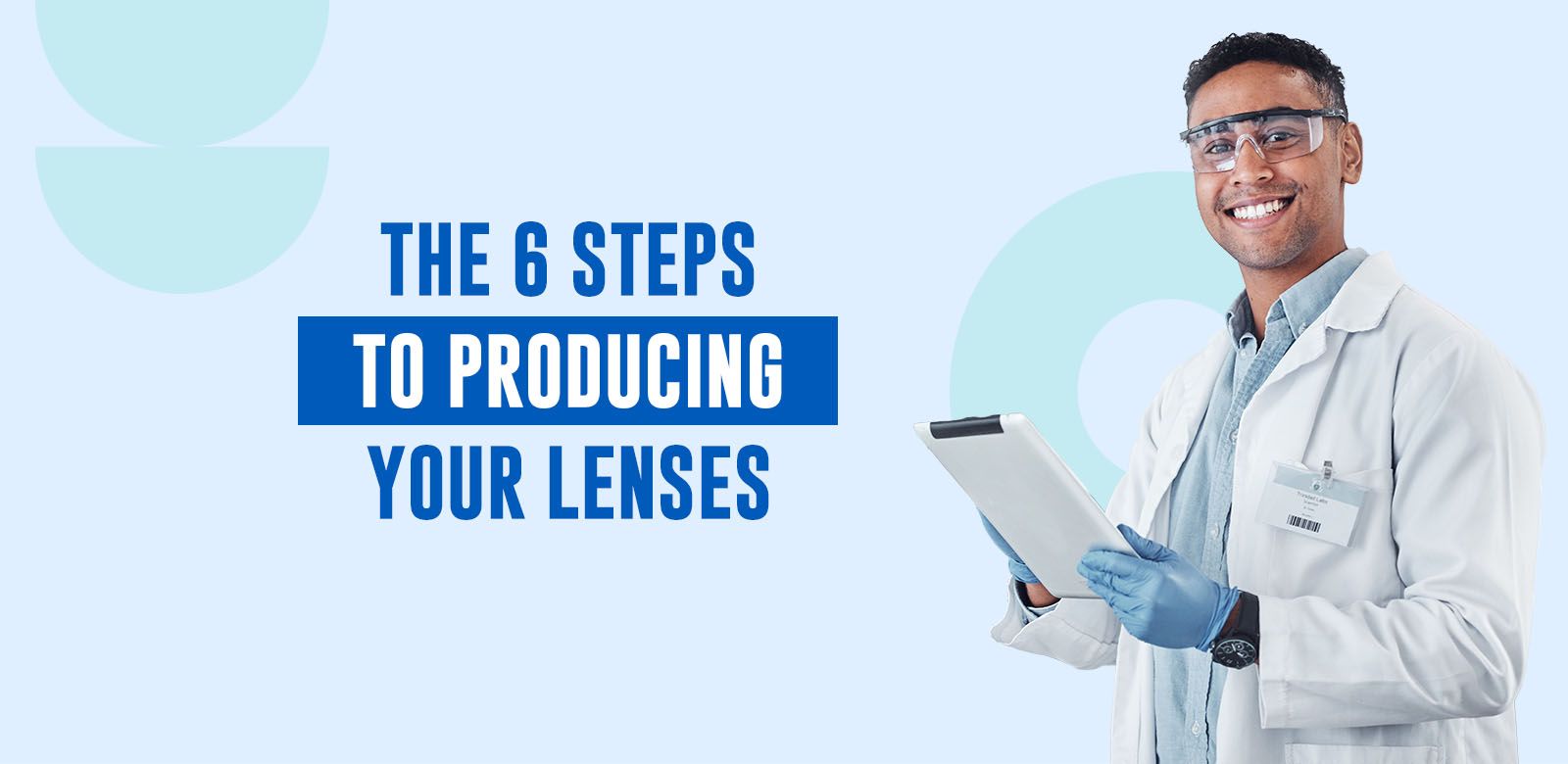
Do you know how your lenses, essential for correcting vision problems like myopia, astigmatism, and presbyopia, are made? Behind each pair lies a complex and detailed process. This article will reveal the behind-the-scenes of lens production, from the initial design and mould creation to quality control, with the aim of providing you with lenses that meet your needs and provide optimal comfort.
Step 1: Selecting raw materials
The first step in designing contact lenses is determining which raw material to use. Most are made from a plastic component, similar to water, specifically designed to be compatible with the eyes. The two main materials used are hydrogel (also called hydrophilic) and silicone hydrogel.
-
Hydrogel contact lenses: These adapt to the shape of the eye and have a natural high water content, providing hydration and comfort throughout the day. Hydrogel lenses are recognisable because they harden when dry and become soft and flexible when hydrated. This technology is often used for soft contact lenses, such as Dailies Aqua Comfort Plus or Biomedics 55 Evolution.
-
Silicone hydrogel contact lenses: The main difference with hydrogel lenses is that silicone hydrogel lenses, such as the monthly AirOptix Plus HydraGlyde or Total 30, offer high oxygen permeability (the amount of oxygen that can pass through the lens to the eye). This significantly improves comfort throughout the day.
Step 2: Design and moulding
Creating the mould
Once the raw material is determined, the next step is creating the lens mould. This mould is essential to ensure that each produced model is unique and meets the defined specifications (comfort and optimal vision).
-
Designing the mould: Engineers will start by drawing the lens using computer-aided design (CAD) software to define its dimensions and shape.
-
Making the mould: Once the design is finalised, the mould is created using precision machines like milling machines and laser cutting machines. These techniques ensure micrometric precision, crucial for the best quality.
Moulding
Once the mould is created, the next step is moulding the contact lenses. This process transforms the raw material into lenses.
Step 3: Polishing
After they are moulded, the lenses go through the polishing stage. This step makes the lens surface smooth and soft.
Step 4: Quality control
They then go through a series of rigorous quality checks to ensure they meet safety and performance standards. There are two types of checks: optical inspection and mechanical inspection. The first check ensures clarity, shape, and aesthetic appearance of the contact lenses, while the second aims to check their resistance and durability.
Step 5: Sterilisation and packaging
Once the lenses are made and polished, they need to be sterilised to eliminate any risk of contamination. After sterilisation, they are hermetically packed in storage solutions to maintain their hydration and sterility.
Step 6: Commercialisation
When contact lenses are polished, have passed quality checks, and are hermetically packed, manufacturers can start marketing their products and sell them to various retailers such as Linsenmax, the contact lens specialist in Switzerland since 2007.